Home » Posts tagged '3d printing design'
Tag Archives: 3d printing design
3D Printing Services
3D Printing Arizona is a fabrication technique that builds three-dimensional objects using layers of materials, like plastics, composites and bio-materials. Also known as additive manufacturing, this technology is making waves in the industry with revolutionary benefits for manufacturers.
Once the CAD model is created and “sliced” into thin cross-sections, the printer takes over. A nozzle deposits the material layer by layer until the object is complete.
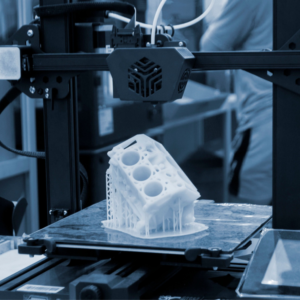
A rapid prototype is a model that can help identify design flaws and improve a product before the final product is manufactured. It is also an effective way to test a product with a limited number of users and can help reduce the time and cost needed to make changes. The term is closely related to the concept of a minimum viable product (MVP) and many designers use both terms interchangeably.
The process of creating a physical prototype using 3D printing involves converting digital designs into tangible objects through layer-by-layer fabrication. The technology offers a wide range of materials to choose from, allowing for experimentation with different design features. For example, a designer can choose to use different shapes, colors and textures to see how these variables affect form and function.
3D printing is a quick and inexpensive method for producing a prototype, which can then be modified as necessary before the manufacturing process begins. This helps companies avoid the high costs and lengthy development time associated with traditional manufacturing methods, such as injection molding or casting metal.
During the prototyping phase, it is important to create prototypes that are as close to the final product as possible. Functional prototypes are often used to demonstrate and validate a product’s functions. Visual appearance is a secondary consideration when creating this type of prototype. Functional prototypes are often created in parallel to allow for testing of various components separately before they are incorporated into a more comprehensive version. This can help developers determine which functions are essential for a successful product.
There are several different 3D printers that can be used for prototyping, including fused deposition modeling (FDM), selective laser sintering (SLS) and stereolithography (SLA). Each has its own set of benefits and disadvantages for various applications. For example, FDM is a popular and user-friendly technology that uses thermoplastic filaments to build models from layer to layer. SLS and SLA utilize powdered material that is sintered or solidified through a laser. Both of these processes can be used to produce both plastic and metal prototypes.
Cost-Effective Manufacturing
With the manufacturing market shifting towards more personalized products and on-demand production, 3D printing finds a range of uses. 3D Printers can be used to produce prototypes, spare parts or finished products at a fraction of the cost associated with traditional manufacturing processes. The technology also helps reduce costs throughout the entire workflow, from design and product development to production and warehousing.
The most obvious benefit of 3D Printing is that it can be used to create a wide variety of complex, custom shapes without the cost and time involved in modifying existing tools or building new molds. This translates to shorter lead times and lower labor costs, which in turn can significantly decrease production and shipping costs.
One of the most significant cost savings comes from the fact that the printing process produces very little material waste. The printing method dispenses raw materials layer-by-layer, so only the amount that is needed is added to the final object. This makes it far more resource-efficient than subtractive manufacturing methods, which often generate large amounts of scrap material.
Another major source of cost reduction comes from the ability to make iterations of a prototype much more quickly and cheaply than with traditional methods. Since a 3D printed prototype is based on digital CAD data, it can be easily modified and reprinted to test different design options – and to correct mistakes. This can accelerate the product development phase, reducing overall cost and risk of costly errors.
3D printing can also be used to reduce the number of components in a product. This can save on labour costs during assembly, and it may cut down on maintenance costs. It can also make it easier to ensure that mating surfaces fit together correctly, reducing the potential for leaks or damage.
The printing process can also be used to produce parts that are extremely lightweight and strong. Using plastic materials like PETG and ABS, or high-performance carbon fibres, manufacturers can experiment with designs that would be very difficult to make with conventional methods. This enables them to create innovative products that are lighter and more durable than the competition, without having to sacrifice performance or price.
Lightweight and Stronger Parts
3D printing allows for the creation of lightweight and strong parts that can be used in a wide range of applications. Creating strong and durable parts requires careful consideration of the materials, printer settings, part orientation, and internal structure of the printed object.
The strength of a printed object depends on its mechanical properties, such as its tensile strength. This property is measured in megapascals, which is a unit of measurement equal to one million newtons of force per square meter. There are several different ways to increase the strength of a print, including tweaking the printer settings and applying post-processing techniques. Among the most effective methods is annealing, which involves heating the part to re-organize its molecular structure. This makes the print stronger and less prone to warping.
Another way to make prints stronger is through a process known as chemical dipping. This is a complex process that involves the use of caustic chemicals and should be performed by trained professionals in facilities with proper safety equipment. This technique can improve the strength of plastic, metal, and concrete prints by bonding them together with a coating that is more durable.
Designing a part for strength is essential when using 3D printing, especially for load-bearing parts. Carefully thought out CAD designs can reduce stress points by distributing loads evenly across the surface of the part. Avoid sharp corners, which concentrate stress and can lead to cracking, and reinforce critical areas with ribs and gussets. Choosing an infill pattern that maximizes mechanical strength can also be very beneficial. Examples of high-strength infill patterns include cube, gyroid, and hexagonal.
For the strongest possible printed objects, it’s important to select a quality material that is suitable for your application. 3D printing can be done with a variety of materials, ranging from elastic plastics to heat-resistant metals. A quality material will be able to withstand the required amount of pressure for your specific project, while also providing the best combination of strength and durability. For example, you may need a more flexible plastic for prototyping, while a harder plastic will be better suited for end-use products.
Customization
Customization is an important part of the 3D printing process that allows for individual creativity. This makes it ideal for producing customized products for a range of applications, from fashion where personalized jewelry pieces stand out to the automotive industry where customizable car parts are improving vehicle performance and aesthetics. It’s also transforming the medical field, where custom-made implants are providing improved patient outcomes and a more comfortable experience for patients.
Traditional manufacturing relies on standardized molds and assembly lines to churn out identical products in bulk, which limits the degree of customization that can be achieved. However, additive manufacturing eliminates the need for molds and enables manufacturers to produce items on-demand, which opens up a world of possibilities for customization at scale. In addition, the flexibility of 3D printing reduces production costs by lowering materials and assembly costs, as well as cutting down on tooling, set-up, and labor expenses.
A number of software programs are available for creating 3D designs, from basic models used in education to complex designs intended for industrial manufacturing. Some are free, while others come at a premium price. Identifying the objectives and intended purpose of the design will help users choose the best program for the job. User-friendliness, compatibility with CAD software, and plugin support are additional features to consider.
Whether designing for 3D printing or simply wanting to visualize print-outs, G-code analyzer and other free tools provide the ability to view and verify the instructions of a printed object before beginning the process. Other software, such as ideaMaker and Simplify3D, offer a more comprehensive approach, with user-friendly interfaces and advanced features that enable users to adjust specific parameters and achieve desired results.
A growing number of printers are capable of printing multiple materials, including metal. For those seeking to use 3D printers for commercial production, it’s important to work with a provider that offers a wide range of materials, from neat polymers and engineering-grade thermoplastics to more durable composite materials that can be used in end-use applications. The versatility of these materials enables manufacturers to produce more sophisticated products, reducing the time-to-market for new products and expanding their market reach.